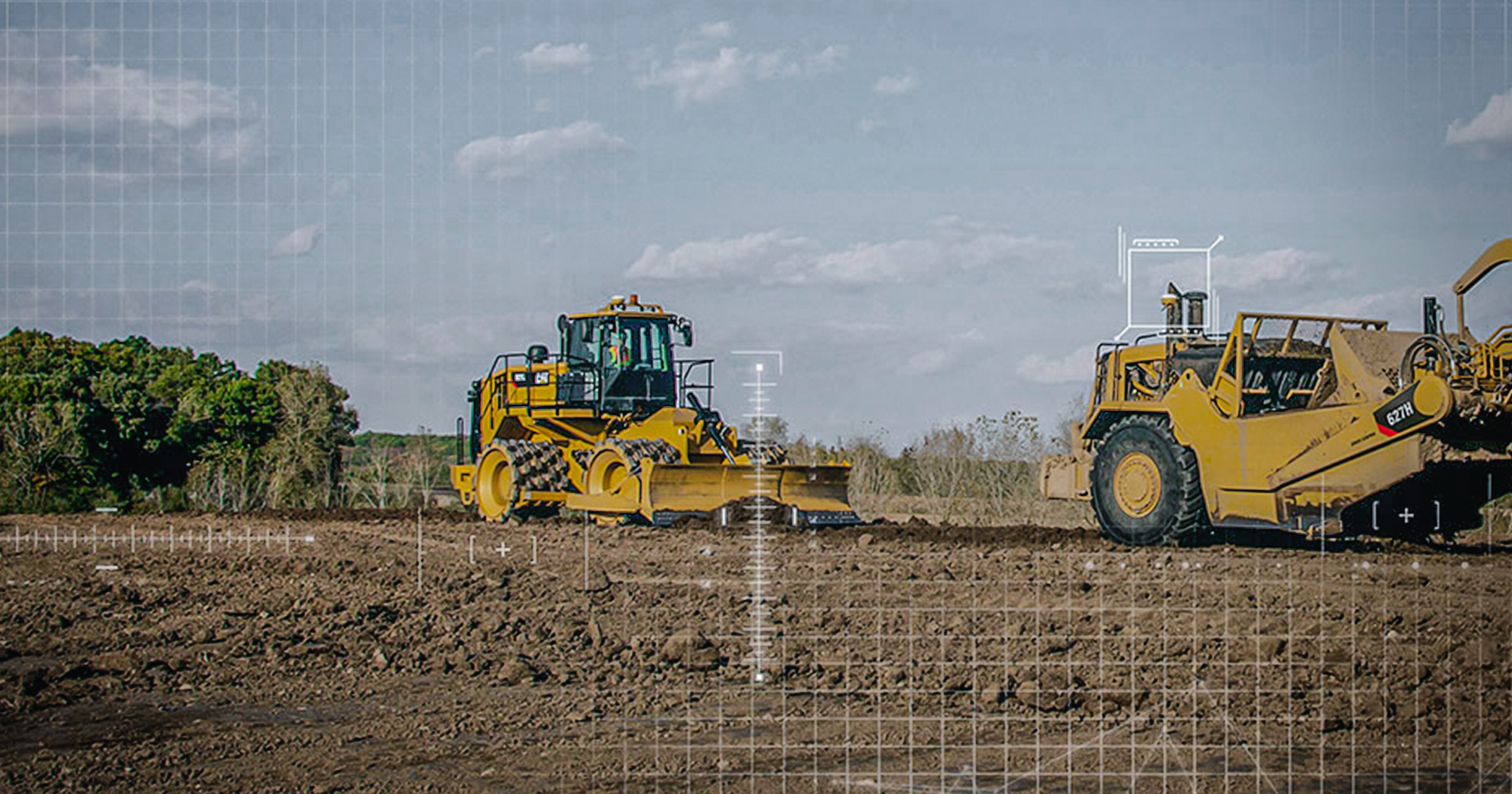
With over 21 years of experience in robotics, manufacturing, remote monitoring, and equipment management, Dan Martin is Corporate Equipment Management Services Manager. For the past four years, he’s been the one handling all heavy equipment solutions for effective maintenance and repair programs, machine safety programs and equipment use on jobsites. Dan agreed to answer questions about his job and telematics.
What are the key types of information that our technologies share with fleet owners?
We have a spectrum of solutions to help customers of all sizes. We have everything from landscaping crews who own a single skid steer loader all the way up to multinational mining customers.
A smaller operation might want to keep track of where their equipment is and when it was running. A slightly larger company might start getting into tracking idle time and fault codes so they can better plan their maintenance intervals.
The largest customers generally focus on site performance metrics such as payload data, utilization, compaction, and volumes moved. Their equipment is often connected through wifi or other high-speed connections so we can monitor sensor-level data by the second. We can often detect problems before a fault code has been generated by the machine’s computers.
How do our technologies help fleet owners to practice preventive and predictive maintenance?
The old “run it ‘till it breaks” mentality is the most expensive way to own and operate a machine. Switching to a routine preventive maintenance schedule is the quickest and easiest way to reduce your costs and ensure your equipment won’t let you down.
We have several tools to help even the smallest shops run an effective maintenance schedule. My first advice is to let the machines do the planning for you. Our ProductLink technology combined with VisionLink or My.Cat.Com sites will automatically track what service is coming up next. A parts list is included with every service interval, so you don’t have to look up what filters and gaskets need to be replaced. We can even ship a complete service kit to you or have one of our PM techs perform the service at your site when you’re not using the machine.
Predictive maintenance is the newest evolution. It’s really the “Holy Grail” of machine maintenance practices because it provides the lowest running costs while maintaining the highest machine availability. It’s really a marriage of tried-and-true maintenance practices like regular fluid sampling and inspections coupled with some smart systems (and people!) to identify what should be done at the next service.
One of the benefits of being a part of the Caterpillar dealership network is we have access to a global community of Condition Monitoring Analysts who are monitoring the same equipment working in similar conditions. Having access to wear tables and component life expectancies in various conditions really gives us an advantage.
With the huge amount of data available, how do you assist customers with what is best and most important for their operation?
If you’re just starting out with monitoring your equipment, I can recommend downloading the Toromont Connect app on your phone. This app will give you a good summary of machine data right in the palm of your hand. We have a companion site called Toromont Hub that is best browsed from your laptop.
Those who are looking for more machine data should check out VisionLink or My.Cat.Com. VisionLink is the preferred platform for those who need the most up-to-date data to run their business. It also has custom reports that can be emailed to you and alerts that can be sent to your phone.
Of course, there’s also the option of letting us monitor your fleet for you. Our Condition Monitoring Analysts are great at filtering out the “noise” and alerting you only when there’s something that requires your attention. We can provide custom reports or even attend regular meetings to update you on the condition of your fleet. It’s a true partnership between our organizations.
What would you say to fleet owners who think they can’t afford telematics systems? Are they more affordable for small fleet owners?
The good news is it has never been more affordable to connect a fleet. We have a ton of retrofit options that work on Cat and other manufacturers equipment. We have everything from basic location-only tags that can track small work tools, all the way up to fully integrated systems that can read all available machine data. There’s something available at every price point.
Another piece of good news is almost every new machine we’ve sold in recent history is connected from the factory. Your machine might already have the hardware it needs to get connected. Get in touch if you’d like us to review your fleet to see what it would take to get you connected.
Lastly, if you already have some of your fleet connected through another manufacturer, we can likely import that data into our platform without having to retrofit any additional hardware to your machine.