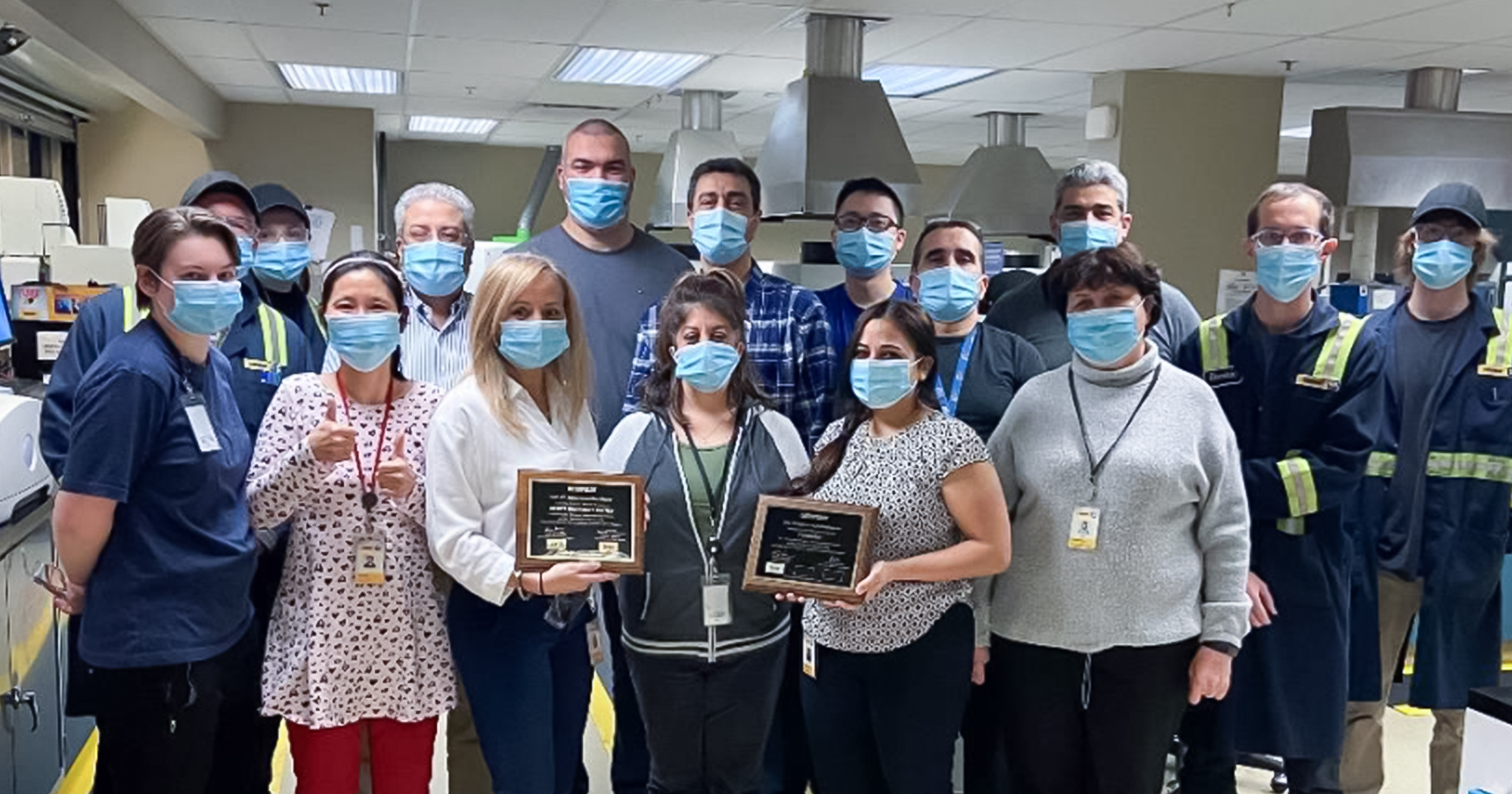
Unforeseen equipment failures and sudden disruptions on a worksite can be costly. What if there were a solution to diagnose potential equipment problems before costly repairs are needed?
The Fluid Analysis team at Toromont can do just that, at any stage of the equipment’s lifecycle. Samples of oil and fluid provide an overview of the equipment’s overall condition. By analyzing test results, the team can detect problems long before they arise and make clear recommendations to improve the situation. Djaouida Takouk, Fluid Analysis Laboratory Manager, introduces us to these specialists, whose role is essential for proper equipment management and Customer Value Agreements (CVAs).
What is your team’s role at Toromont?
The team at the fluid analysis laboratory plays a crucial role. From a sample of oil, coolant or diesel fuel, they gather the technical information essential for protecting a piece of equipment. Indeed, fluid analysis is the quickest and most reliable way to see what’s going on inside an engine or piece of equipment.
For example, a chemical technician uses analytical instruments such as an atomic emission spectrometer to identify and measure metals, contaminants and additives in the oil. This helps determine whether equipment wear is normal or abnormal, and enables the user to make preventive diagnosis in order to avoid a major breakdown and work stoppage.
Can you introduce us to your team? How many people work at the Pointe-Claire laboratory and what are their roles?
Our team is made up of 15 technicians, one coordinator and me.
Each technician works on one stage or another in the overall process, whether this involves receiving, registering or analyzing samples.
The coordinator is responsible for assigning tasks and technicians. She keeps track of the supplies of consumables and reagents, and acts as a link between the laboratory and the departments responsible for interpreting results.
As the manager, I’m responsible for the laboratory’s day-to-day operations. My role is to create a positive working environment focused on continuous improvement. I make sure new members are properly trained, while identifying each person’s strengths and talents. I also act as a mentor and technical resource for the chemists. In addition, I make sure that the technicians have the appropriate protective equipment and all health and safety measures are observed.
Lastly, I’m always on the lookout for new developments in the market, so that the laboratory can continue to evolve. Today, the laboratory is equipped with the latest analytical instruments. For example, an instrument like the PLC (Particles Liquid Counter) from PerkinElmer is revolutionary for counting particles measuring 4, 6 and 14 microns. Our laboratory is one of only two in North America to own one of these.
How has your department evolved over the years?
Ever since it was set up in 1972, our department has been continually evolving. We now do all our tests in our own laboratory, whereas in the beginning some tests were carried out by subcontractors. The number of technicians has doubled, as has the laboratory’s floor area, and the number of samples processed has more than quadrupled. Samples arrive from all over Canada.
Over the years, we have acquired new analytical instruments that enable us to carry out more precise tests and broaden our range of analysis. We now offer programs for analyzing coolant and fuel.
Among the key developments was the installation of an argon tank, which put an end to frequent shutdowns in order to replace argon cylinders, a gas required for testing.
We have also made it easier to access our services by introducing Cat Inspect and standardizing the SOS kit, which simplifies the sending of samples.
Among the major milestones you’ve achieved, since 2022 your services have complied with the ISO 9001:2015 standard, as well as the prestigious Cat SOS Services standardization 2013-2016-2020. What does this mean for you?
The ISO 9001:2015 standard defines the requirements for a quality management system. In our case, the focus is on data quality and good laboratory practices. Certification confirms our ability to produce valid results that comply with customers’ requirements, thereby strengthening their confidence.
The Cat SOS Services standard indicates that we meet Caterpillar’s high quality standards, which also increases the confidence of our dealers and customers. It’s worth noting that we’re now the fourth largest of the 90 Cat-certified laboratories worldwide.
What’s the working environment like in Toromont’s Fluid Analysis department?
We’re like one big family. Our team is diverse and its members come from all over the world, but they’re all united by the same passion for chemistry.
The work requires attention to detail, good observation skills, critical thinking and the ability to work in a team. You have to be able to listen to others, as everyone takes their turn performing part of the analysis on the same sample.
Our team is also highly disciplined, whether in applying good laboratory practices to ensure data quality, handling samples and using instruments, or meeting deadlines promised to customers. The commitment of all members to their colleagues, the company and customers is beyond reproach.
Contact the Toromont Fluid Analysis Services team
Call: (866) 569-5979
Email: soslab@toromont.com