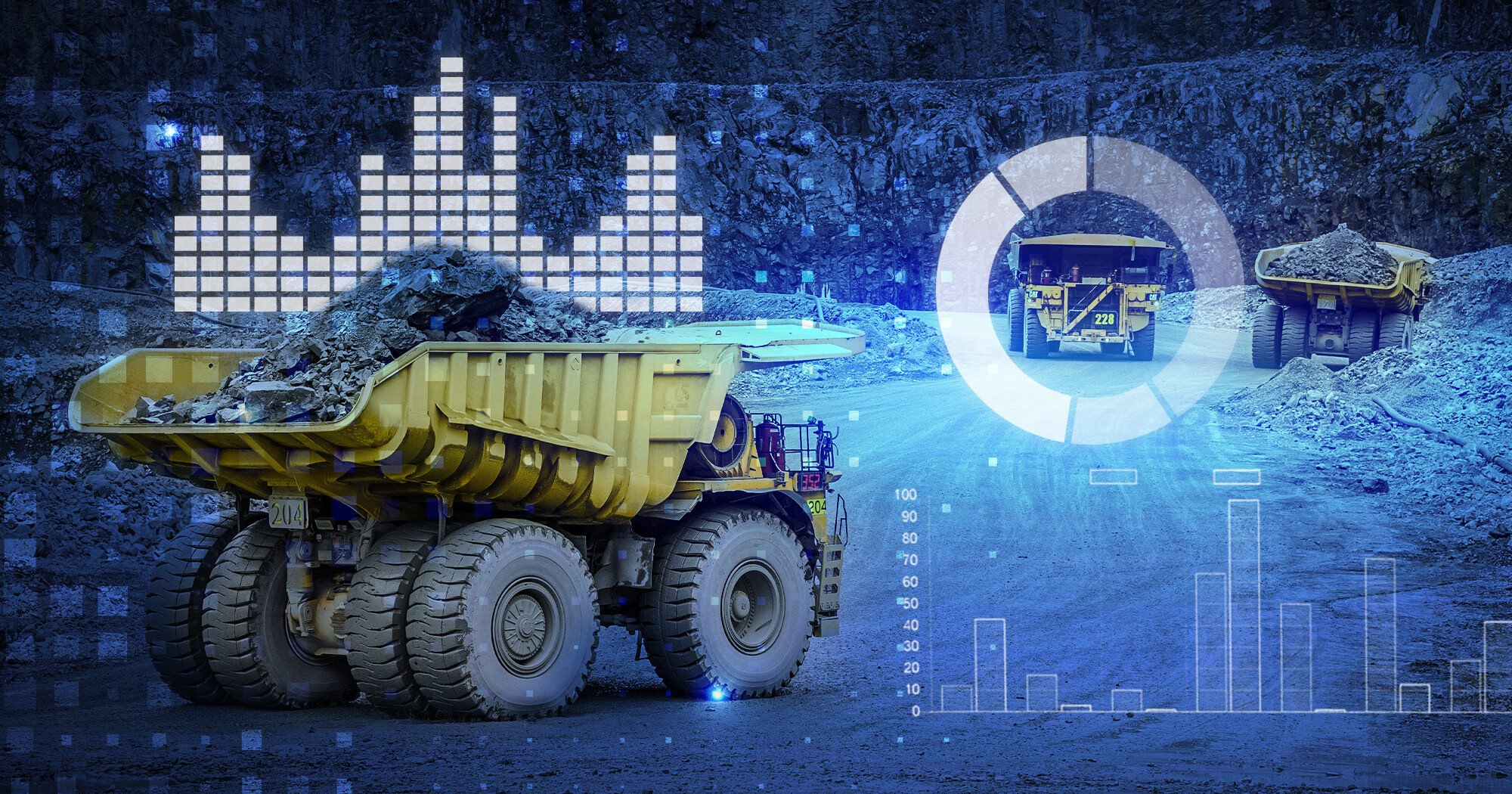
Over the lifetime of your mining operation, you can always find new ways to streamline and reduce costs. But did you know that your biggest opportunity to reduce the total cost of machine ownership comes before the machines arrive on site?
Toromont will work with you to select a perfect fleet that optimizes your investment and lowers your Total Cost of Ownership.
Understanding Your Operation
Fleet selection begins with a discovery phase, when you share as much information as possible about the location and logistics of your mining operation.
First, we’ll need to know about the mine itself, including: the mine location, materials being mined, general weather conditions, ground conditions, the slope and distances of transport routes, and the annual tonnage objectives.
With that information logged in Caterpillar software, the next step is to simulate truck loading and travel times for trucks. This includes forecasting future time requirements as the pit becomes deeper and the number of trucks required to move material out increases.
Additional details required are:
- Mine plan for the life of mine
- One average road profile per year (loading point to dump destination for ore and waste)
- Annual tonnage objective associated with each road profile
- Material loose density (ore and waste)
- Net operating hours per day
- Fuel costs
- DEF costs
- Carbon costs
- Annual operator costs
- Site speed limits
- Intersections and stop signs
Fleet Selection
Toromont’s application engineers will run a variety of fleet simulations to evaluate and determine which one would be the best long-term solution. There are a lot of factors to consider.
Often, a smaller fleet is required for the first years of operation and larger equipment becomes necessary as production increases.
Larger machines may show an improved cost per tonne — but if you have a small fleet population, the impact of having one machine down for maintenance can have a larger proportional impact on your production goal.
Typically, you will need two primary loading tools and a back-up machine, such as a wheel loader. Each loading tool should have a minimum of 3 trucks assigned to it. That way, if one of the trucks is down, the loading tool will still have two trucks assigned.
Ideally, we can narrow your options to just one or two fleet size recommendations with an optimal mix of machines suited to your anticipated needs.
Once the fleet is selected, our application engineers work alongside Toromont Wear Products (Accessories and GET) Specialists to arrive at recommendations for bucket type, bucket size, GET and protection. Truck bodies will be recommended for optimized truck payloads.
There are a few critical things to note:
- A truck’s gross weight is limited by brake and tire certifications — so one tonne of extra GET or additional body wear plates will result in the loss of one tonne of payload.
- That same logic applies to the loading tools, where the wear protection is a compromise between longevity and payload.
- The haul distance will greatly affect the truck body wear, as truck bodies only wear out when the material is being dropped in by impact, and from friction when the truck payload is dumped. Long hauls will have less impact on the body wear because trucks are performing less loading cycles per hour.
- Truck weight and target payload estimates will be documented, in detail, on a sheet from Caterpillar that includes all truck options selected — along with customer-added weight like fire suppression systems.
After Delivery
Once your machines have been delivered, Toromont’s teams will visit the site to verify that everything is performing as expected. This review ensures that the simulations were accurate and that the future fleet analysis can be relied on.
Overloaded trucks can reduce tire life, cause slower speeds on grades, shorten component life, and create higher fuel consumption. The application team will measure:
- The weight of loaded trucks, to confirm the accuracy of the truck onboard scale.
- The real empty weight of trucks, to help calculate the exact recommended payload.
- The trucks’ speed on grade, loading times, dump times, and payloads.
- The load distribution between left/right and between front/rear, to validate load positioning and provide recommendations to the loading tool operator.
Operator practices will also be reviewed by the our training department, and corrective measures will be implemented, if necessary, to further boost efficiency and productivity.
CASE STUDY: Salt Mine Project
A salt mine had a major underground construction project in their mine plan, all of the parameters for a fleet study, and a good idea of what they needed. They approached Toromont to refine their selections and make recommendations that would lower their capital expenditure.
A site visit and in-depth application discussion quickly followed. The customer shared that they were planning to rip compacted salt with a D8 dozer and were considering a 374 excavator to load the ripped material into trucks.
They knew the dozer would have limited use underground once the construction was completed. Also, the dozer would have to be dismantled and reassembled underground, so it wouldn’t be cost effective to bring it back from this site.
"Our recommendations saved the customer more than $1M and eliminated the need for additional equipment and underground ventilation."
- Yves Laquerre, Application Engineer
The Toromont team recommended a 374 with a quick coupler and a ripper attachment that would turn it into a comprehensive multi-tool. The excavator could switch from loading with a bucket to ripping, as the excavation progressed. The team also recommended the addition of a hydraulic hammer to break up any material that proved to be difficult to rip.
These recommendations saved the customer more than $1M and eliminated the need for additional equipment and underground ventilation. Additional fleet analyses were performed for the project, and the collaborative partnership between Toromont and the customer continues today.
Need help choosing the perfect fleet?